- Vapor Barriers for Concrete Slabs
- Concrete Moisture Problems
- Vapor Barrier Installation
- Related Information:
- Avoiding moisture-related problems with concrete sealers: Advice from expert Chris Sullivan
- Reducing bond failures caused by moisture- vapor transmission
- Don't let water vapor delaminate your overlay
- W. R. MEADOWS White Paper - Tips on Choosing Vapor Barriers
- Are concrete floors cold and damp?
- Product Newsletter: Sign up today to receive monthly updates
- Free Vapor Barrier Catalog & Info
Section Sponsor

W. R. MEADOWS
Concrete Vapor Barriers - What Are They?
Minimize water vapor moving through a slab by choosing the right vapor barrier and installing it properlyThe last thing you want your customers to envision when thinking of a concrete floor is a damp, cold basement slab. One of the reasons those old basement floors were like that was because they had no vapor barrier beneath them, leaving an easy path for water vapor from the soil to migrate into the slab, assuring that the cold clammy damp feeling never went away.
And dampness is only part of the problem, water vapor moving through a concrete floor can:
- Delaminate sealers
- Cause overlay bond failures
- Discolor acid stains
- Produce efflorescence on the surface
- Damage aggregates
- Cause the slab to curl
- Condense beneath objects on the floor
But it doesn't have to be that way. On new interior slabs, moisture can be easily controlled and mostly eliminated. Here is information to help you understand how moisture moves in a slab and how using a vapor barrier can help control the problem.
Read more about moisture coming up through concrete, including how to test for moisture vapor transmission.
What are Vapor Barriers?
All of the problems associated with moisture vapor movement in a concrete slab will go away in time as the slab dries, as long as there is no source of additional water into the slab. Since the most common source is moisture in the ground beneath the slab, the solution is to completely take the ground out of the equation, by sealing the bottom of the slab.
Find out where to buy vapor barriers and other problem solving products.
The best way to accomplish that is with a vapor barrier under the slab. Vapor retarders have been used since the 1950s. Recently, though, research has shown that the old traditional layer of 6-mil Visqueen (polyethylene plastic) under the slab is seldom effective for two main reasons:
- Although it may seem water-tight, this grade of material allows a lot of water vapor to pass through.
- 6-mil plastic often gets damaged during placement of reinforcement and concrete, creating holes that can let a considerable amount of water vapor into the slab.
Thin plastic like this is often called a vapor retarder—meaning it slows the vapor down but doesn't stop it. A much better approach is a true vapor barrier, with characteristics that conform to the requirements of ASTM E-1745, "Standard Specification for Water Vapor Retarders Used in Contact with Soil or Granular Fill under Concrete Slabs." This specification has three classes of vapor retarders (or barriers--the terms are still often used interchangeably), Class A, B, and C.
For all three classes of vapor retarder, the permeance (a measure of how much vapor can pass through) must be less than 0.3 perms. Most experts today don't think that's low enough, and a few materials have recently become available that have permeance values less than 0.03 perms—some as low as 0.01. These low permeability materials completely eliminate any moisture migration from the ground, allowing the slab to dry out much more quickly and to stay dry. ACI 302.2R-06, Guide for Concrete Floors that Receive Moisture-Sensitive Flooring Materials, estimates that concrete with a w/c of 0.5 will dry to an MVER of 3 pounds/1000 sq. ft/24 hours in 82 days with a vapor barrier, compared to 144 days when exposed to vapor from below.
The other characteristic of a good vapor barrier that makes it effective is resistance to punctures and tears. ACI 302.1, Guide for Concrete Floor and Slab Construction, states that the minimum thickness of an effective vapor barrier is 10 mils. This was verfied by some field studies conducted by Concrete Construction magazine. Thinner plastic can't stand up to the abuse of construction. ASTM E-1745 specifies minimum values for tensile strength and puncture resistance that increase from Class C to Class A.
A 10-mil vapor barrier may be sufficient for residential construction in terms of puncture resistance, although the 10-mil barriers can't completely isolate the slab from ground moisture. The newer very low permeability barriers, such as those from W. R. MEADOWS, Fortifiber, Interwrap, Raven, Reef, Polyguard, Stego, Grace Construction Products, Strata Systems, and Layfield are 15 mils (15 thousandths of an inch) or greater. This thicker material is much less susceptible to tears or punctures and has a lower permeance.



Choosing a Vapor Barrier
- Bottom line: If you want to make sure your slab on ground gets dry and stays dry, use a vapor barrier.
- Cure with waterproof sheets rather than with water or curing compounds.
- All vapor barriers should conform to ASTM E-1745; but consider going with a barrier that has water vapor permeance less than 0.3 perms.
- A 10-mil barrier is probably OK for residential construction if you're careful not to puncture it during construction.
- If laser screeds or heavy placing equipment will be on the barrier, go with 15 mils.
- Starting with lower water-cement ratio concrete will let the slab dry faster. Keep w/c at or below 0.5.
- Vapor barriers also block gases, such as methane or radon. Radon is the second leading cause of lung cancer in the U.S., according to the American Lung Association.
- Typical 8-mil polyethylene sheeting costs 5 to 7 cents per square foot. A 15-mil vapor barrier can be about 25 cents per square foot. Sure, that's an increase, but it's better than a damp, discolored slab.
- Get tips on choosing a vapor barrier in this white paper from W.R. Meadows.
- Learn how to install a vapor barrier
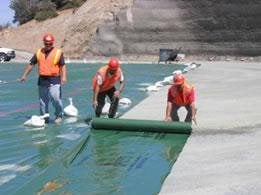
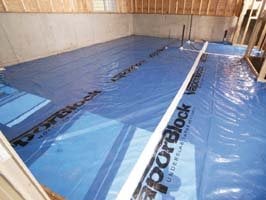
acceptable. Raven Industries in Sioux Falls, SD