- GFRC Home
- Benefits of GFRC
- Design Ideas for GFRC
- Applications for GFRC
- Countertops
- Fireplace Surrounds
- Architectural Accents
- Faux Rock
- Mixes and Materials for Making GFRC
- Glass Fibers for GFRC
- Mixes and Materials for GFRC
Glass Fiber Reinforced Concrete
How to use GFRC for better decorative panels and countertopsWhen someone says fiberglass, we think of insulation or boats or Corvettes, but maybe we should think of concrete. Technically, fiberglass is simply very fine glass fibers. The material used to make boats or other products, although called fiberglass, is really glass fiber reinforced plastic-glass fibers in a polymer matrix. If, instead of the polymer, we use portland cement and sand, the resulting material is glass fiber reinforced concrete--GFRC or sometimes GRC (the Brits call it glassfibre reinforced concrete).

GFRC can be used to create durable and exquisitely detailed ornamental concrete. NEG America

Countertops with integral sinks remain crack free when made with GFRC. Concast Studios in Oceano, CA

Artificial rocks made with GFRC look real at a fraction of the weight. Innovative Rock & Water
The problem with using glass fibers as reinforcement for concrete is that glass breaks down in an alkaline environment--and there's almost nothing more alkaline than concrete. You may have heard of concrete being damaged by alkali-silica reactivity (ASR) when there is reactive silica in the aggregate. Glass is primarily silica. The original GFRC in the 1940s rapidly lost strength as the glass was destroyed by the alkaline environment. In the 1970s alkali-resistant (AR) glass fibers were perfected by Owens-Corning and by Nippon Electric Glass (NEG) leading to a rapid increase in applications.
Find Supplies: GFRC Mixes
GFRC has been used for the past 30 years to produce many concrete products, especially thin architectural cladding panels, but also for ornamental concrete such as domes, statues, planters, and fountains. Recently, decorative concrete artisans have discovered the benefits of GFRC for decorative panels (such as fireplace surrounds), concrete countertops, and artificial rock work.
MANUFACTURING GFRC PIECES

Larger architectural elements are created by directly spraying the premixed GFRC into a mold. NEGAmerica
There are three methods for making concrete elements using GFRC: traditional hand spray-up, vibration casting, and sprayed premix.
- The traditional, and perhaps still the best, way to manufacture precast GFRC elements is by hand spraying the GFRC into a mold. This is how most precast GFRC architectural cladding panels are made and also most ornamental precast GFRC. With the direct spray-up method, you need a concentric chopper gun, which is fed by a spool of GFRC roving pulled into the chopper gun and blended at the nozzle. This mix has a higher fiber content (4 to 6%) than can be achieved with premix and is the recommended method for larger panels. It does, however, require experienced workers, expensive equipment, and rigorous quality control.
- Vibration casting uses premixed GFRC poured into a mold and vibrated to achieve consolidation. This is a much simpler method, but requires water-tight molds and doesn't work well with rock molds.
- Sprayed premixed GFRC, with chopped fibers in the mix, requires a peristaltic pump and a special spray head. This method requires less expertise than the hand spray-up method and results in higher strengths than with vibration casting.
Find contractors who work with GFRC near me.
Most decorative GFRC pieces, especially countertops, or fireplace surrounds are made using a two-layer approach. The facing layer is the thin decorative layer and the backup layer is thicker and contains the glass fibers.
- The face coat is normally sprayed into the mold using a drywall hopper gun. This layer is about 1/8 to 3/16 inch thick.
- "One square foot of countertop requires only about 2 pounds of concrete mixture for the face coat," said Mike Wellman, Concast Studios, Oceana, Calif. "It's pretty thin so with my mixer I'm able to do a 200 square foot job--about the biggest kitchen there is. This allows me to do the whole thing with one batch to insure color consistency."
- "We let the face coat set to where it's moist but won't move-about ½ hour to 1 hour," said Wellman.
- The GFRC backer coat is then placed. Most decorative contractors either pour this layer or trowel it on by hand. The thickness of this layer is in the range of ¾ to 1 inch, depending on the size of the panel and the loads it will be carrying.
- The GFRC layer is typically placed in two layers of about 3/8 inch and compacted using rollers or a vibrating table.
- Mixers for GFRC need to provide a lot of shear at both low and high mixing speed-high for the low water-cement ratio concrete mix then low to prevent breakage when the glass fiber is added. Power-Sprays is a British company, represented in the U.S. by NEG America, that specializes in GFRC equipment. They make an excellent upright mixer. You can also use a handheld mixer, such as those from Collomix or even a mixer blade on an electric drill. "The limitation for most guys is having a mixer that can mix enough volume and has the power to mix fiberglass in well," said Wellman.
- With the polymer addition, GFRC sets fairly quickly. Depending on conditions, panels can be stripped and polished within 24 hours, although Wellman waits 3 days for the concrete to gain nearly its full strength

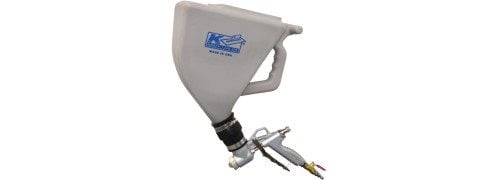

Find Local Suppliers: Decorative Concrete Stores
MAKING GFRC DECORATIVE
GFRC panels can be given nearly any decorative treatment as normal concrete. The application dictates what works best:
- Architectural panels are often cast using various form liners. The surface finish can be sand blasted, acid etched, or polished. Various tints of gray, white, and buff can be achieved using colored cements or pigments.
- Many GFRC ornamental pieces are shot or cast using white cement and light color tints. Stone or clay brick pieces can be embedded in panels, although consideration should be given to the differential shrinkage characteristics of the different materials. Many different architectural features are best produced using GFRC.
- Countertops are typically made using a face coat and a solid integral color is often the method of choice. "We use integral color in the face coat," said Mike Wellman, Concast Studios, Oceana, Calif. which makes countertops and fireplace surrounds. "Sometimes we will do an acid stain but the majority of our clients stick with the straight integral color." Wellman typically polishes the countertop to a high gloss finish, but offers many varieties. Read more about Concast Studios' work.
- Countertops can be produced without the facing coat, although if polished the fibers will be visible. "Some of our customers like the fibers to show," said NEG America's Mike Wellman. "If it's acid etched or acid washed, they don't mind the fibers and they actually blend in with the color."
- With face coats, broadcasting aggregate or embedding decorative elements is a good choice. "Since I'm spraying in the initial face coat I'm able to broadcast aggregate in which lets me get flowing movement," said Wellman. "I can sprinkle in glass or seashells and when polished and exposed it gives the illusion of movement. With wet cast it's trickier to get that movement and make it look good."
- Rock features typically use GFRC panels that are sprayed against molds made using real rock features. Steve Holmes, vice president of Eldorado Wall Company, a Boulder, Colo. maker of rock climbing walls, says that the first coat they spray has no glass fiber. "The chop gun has mud-only and mud-and-glass triggers. The first thin coat has no fibers then we bring the thickness up to ¾-inch nominal with the GFRC mix."
- To create rocks, the GFRC panels are mounted on a structural steel framework. "The panels can be oriented in different directions," said Eldorado Wall's president John McGowan, "then we plaster the seams and sculpt them to blend the panels into a rock feature." To create the patches, said Holmes "we place lath and rebar into the seams then start with a scratch coat then apply the sculpt coat. This is done with a field mix based on a shotcrete recipe." Coloring the rocks is done with a variety of techniques Eldorado has developed over the years.
- Jim Jenkins of JPJ Technologies teaches artificial rock making. His method, however, does NOT use GFRC but rather a composite fiber-reinforced polymer concrete material that he invented and has perfected. "Our panels are ¼ to ½-inch thick," said Jenkins, "where a GFRC panel will be 1-1/2-inch thick. Our material can be cut easily with a circular saw and yet is stronger than GFRC. The seams between panels are patched with the same material used to make the panels so they behave, look, and stain the same." A sister company, Synthetic Rock Solutions, sells premanufactured rock panels that can be used to assemble rock features.
- Coloring rock and water features entails a lot of artistry. Multiple colors and techniques are blended to produce realistic color, as described in "Geo-Illusions" in the December 2007/January 2008 issue of Concrete Décor.
- Ornamental GFRC fireplace surrounds have become very popular, due to their light weight and durability. Check out what Sierra Concrete Designs does with this application in the article Surrounding Fireplaces With Beautiful Decorative Concrete Work.
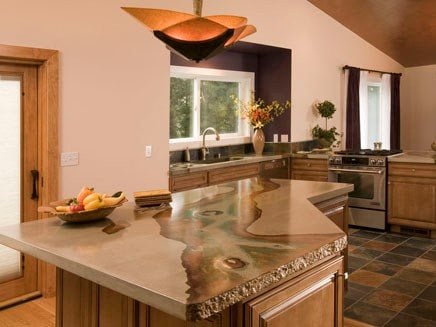
GFRC countertops can be finished using virtually any decorative concrete techniques. Absolute ConcreteWorks in Seattle, WA
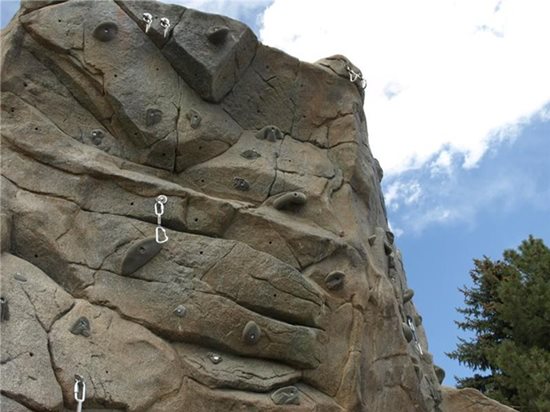
Although the structure for this climbing wall has all of the appearance of real rock, modular handholds are attached for climbing. Eldorado Wall Co.
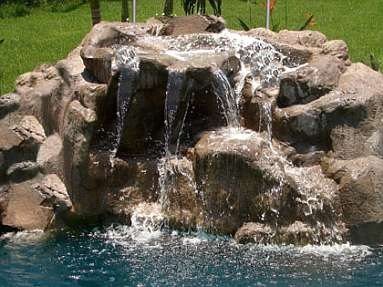
Artificial rocks require artistry in color application to obtain a realistic appearance. Synthetic Rock Solutions in Amity, OR
RELATED:
Concrete Reinforcement for Slabs